Joel_BC
Super Self-Sufficient
Here's a home-made tool thats made from a pair of vise-grip-type pliers combined with a slide hammer. (I'm indebted to Stan Campbell at ToolFools for telling me about this type of tool modification. http://www.toolfools.com/forum/index.php) There are quite a few illustrations on the internet from guys who've made these, but I feel this guy has come up with a very good basic design and has "tested" the tool roughly with much use.
http://www.advrider.com/forums/showthread.php?t=622122&highlight=vise+grip+slide+hammer&page=2
He explains his method of constructing it pretty well on that page.
One reason I like it is that he gives a fair amount of design/fabrication detail. And also he attests to the durability of the tool, in the way that he made it.
He posts about his slide hammer again on this page:
http://www.advrider.com/forums/showthread.php?t=798000
I'm thinking about making one of these, and one question I've got is: where can you obtain a heavy steel object to use appropriately for the slider? With luck, maybe you find an old slide-hammer slide. (Where I live, the used-tool stores and pawn shops have become fewer, and inferior.) But this fellow uses an old "sledge" head. Disadvantages: the hammer head would be forged steel with hardened ends - possibly hard to find just the right old tool to make it from, and definitely slow to drill. Instead of drilling-out an old hammer head, I've got another idea for the slider.
Why not a stack of washers? - good, flat. unbent ones of uniform outside diameter. Make a stack of the right inside-diameter washers, with enough washers to make the slider sufficiently heavy. Then maybe braze or weld thin steel strips at two or three points around the outside to unify the stack. Then maybe inner-tube rubber or even duck tape around the outside to smooth the surface for gripping.
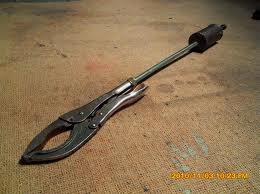
http://www.advrider.com/forums/showthread.php?t=622122&highlight=vise+grip+slide+hammer&page=2
He explains his method of constructing it pretty well on that page.
One reason I like it is that he gives a fair amount of design/fabrication detail. And also he attests to the durability of the tool, in the way that he made it.
He posts about his slide hammer again on this page:
http://www.advrider.com/forums/showthread.php?t=798000
I'm thinking about making one of these, and one question I've got is: where can you obtain a heavy steel object to use appropriately for the slider? With luck, maybe you find an old slide-hammer slide. (Where I live, the used-tool stores and pawn shops have become fewer, and inferior.) But this fellow uses an old "sledge" head. Disadvantages: the hammer head would be forged steel with hardened ends - possibly hard to find just the right old tool to make it from, and definitely slow to drill. Instead of drilling-out an old hammer head, I've got another idea for the slider.
Why not a stack of washers? - good, flat. unbent ones of uniform outside diameter. Make a stack of the right inside-diameter washers, with enough washers to make the slider sufficiently heavy. Then maybe braze or weld thin steel strips at two or three points around the outside to unify the stack. Then maybe inner-tube rubber or even duck tape around the outside to smooth the surface for gripping.